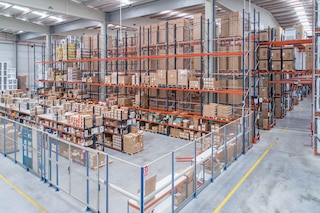
¿Cuáles son los criterios de ubicación de existencias más utilizados en el almacén?
El objetivo de la gestión de ubicaciones en el almacén es colocar el producto adecuado en el lugar correcto para que pueda ser recogido eficientemente en el momento oportuno.
Para ello, los criterios de ubicación de existencias en el almacén determinan la forma de organizar los productos en cada localización. ¿Cuáles son los más empleados? ¿Qué factores debes considerar para optar por uno u otro? Lo vemos en detalle.
Criterios de ubicación de existencias más habituales
Destacamos dos tipos de reglas:
- Criterio de ubicación de existencias fijo o específico: a cada SKU almacenado se le asigna una posición concreta de antemano. Esto facilita la localización de los productos sin necesidad de tener un sistema informático que lo registre.
- Criterio de ubicación de existencias caótico o aleatorio: las referencias se van colocando en los huecos disponibles a medida que son recibidas en el almacén. Para llevarlo a cabo con éxito, resulta indispensable usar un sistema de gestión de almacenes.
Hay que mencionar que, en muchas instalaciones de almacenaje, se aplican criterios de ubicación de existencias mixtos que combinan ambas formas de organizar los productos.
¿Cómo determinar los criterios de ubicación de existencias del almacén?
Emplear un criterio de ubicación de existencias frente a otro va a depender principalmente de tres grandes cuestiones:
1. Estudia las características de las referencias almacenadas:
- Las características físicas de los productos: el volumen que ocupan (medidas de largo, ancho y alto) y su peso son imprescindibles para conocer el espacio necesario para maniobrar y así calcular los sistemas de almacenaje más adecuados. Por ejemplo, los productos más pesados irán emplazados en la zona baja de los racks siempre que sea posible. Se recomienda utilizar un método común, preferiblemente automatizado, para medir cada producto y evitar posibles desviaciones. Así pues, es habitual designar ciertas medidas estándar de cajas en las que cualquier referencia encaje para simplificar el proceso de embalaje.
- Otras características que afecten al almacenaje y ubicación de referencias: se suelen considerar, entre otras, la compatibilidad con ciertas referencias a la hora de depositarlas en la instalación (el almacenamiento de productos químicos está regulado por ley), la resistencia a la intemperie (el emplazamiento en almacenes a cielo abierto puede abaratar costos) o la caducidad en productos perecederos (hay que ordenarlos por fecha, en condiciones concretas de temperatura y humedad, y debiendo figurar el lote como medida de trazabilidad logística).
2. Analiza los sistemas de almacenaje disponibles y la distribución del espacio en el almacén
- Define una nomenclatura que identifique todas las ubicaciones: cuanto más detallada sea, más compleja, pero también más precisa. Como mínimo, la nomenclatura debe incluir la identificación con números o letras de: los canales o estantes, de cada nivel en altura y de cada hueco; pero también se pueden añadir otras dimensiones como almacén, pasillo, contenedor o zona.
- Calcula la capacidad de almacenaje y la ocupación del almacén: si supera el 90%-95% conviene revisar los criterios de ubicación de existencias para ver si se está aprovechando el espacio de la forma idónea. Hay que contemplar también el tipo específico de rack industrial, en especial si se trata de sistemas por compactación o de acceso directo. En general, los primeros se ajustan mejor a inventarios con muchos tarimas por referencia, mientras que los segundos son más versátiles cuando se gestionan pocas tarimas por cada una de ellas.
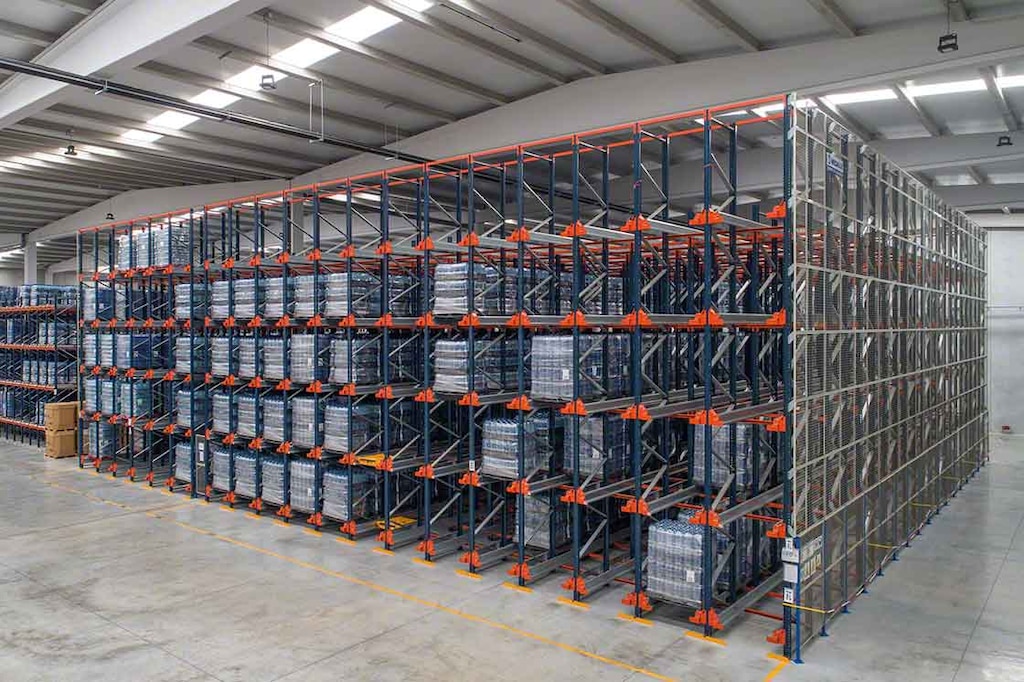
3. Examina los movimientos de mercancías y de operarios en la instalación
- Movimientos de mercancías:
1. Rotación de existencias: permite ordenar los productos almacenados por la frecuencia con la que se les da salida en el almacén. Esto se halla en relación directa con la demanda a lo largo del año. Siguiendo el método ABC, el criterio de ubicación de existencias general consiste en posicionar aquellas mercancías de mayor rotación más cerca de los muelles de entrada-salida e ir avanzando hacia ubicaciones más lejanas a medida que se reduce la rotación.
2. Métodos FIFO o LIFO: hacen referencia al orden que toma el flujo de mercancías. El FIFO (First In, First Out) consiste en dar salida primero a aquellos productos que caducan antes, de ahí que se siga la secuencia “primero en entrar, primero en salir”. En cambio, el flujo LIFO (Last In, First Out) implicaría que el “último en entrar es el primero en salir”.
- Desplazamientos de los operarios:
La distancia recorrida por cada operario depende principalmente del método de picking que se esté aplicando, de la accesibilidad de los productos en las estanterías y de los equipos de manutención y sistemas automáticos. Por ejemplo, los transportadores o los transelevadores disminuyen las maniobras manuales y los recorridos que tienen que realizar los operarios.
La gestión de ubicaciones persigue maximizar la capacidad de almacenaje, minimizar los movimientos y adecuar cada ubicación a las características de los productos.
Gracias a nuestro software Easy WMS, podemos llevar a cabo un análisis en profundidad de las normas de ubicaciones en tu almacén y así optimizar el inventario. Contacta con nosotros y te ayudaremos a definir los criterios de ubicación de existencias que mejor se adecúen a tu instalación.